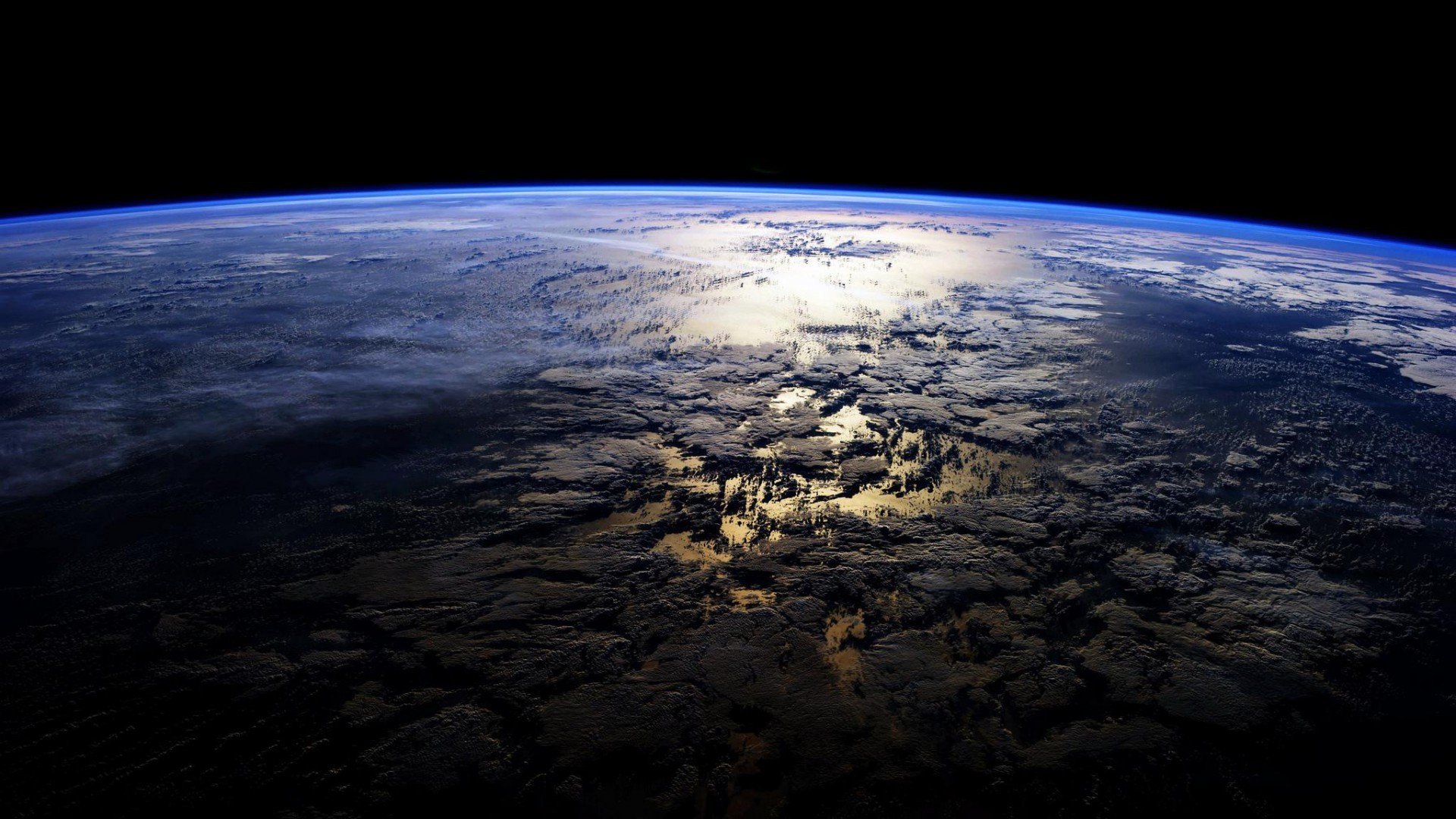
Sierra Space Net Launcher
Capstone Project
As part of a senior capstone with Sierra Space, I helped develop a multi-mechanism debris net launcher designed to identify, capture, damp, and retrieve unresponsive orbital debris. I led the mechanical and systems development of the damping subsystem, integrating sensor-driven controls, solenoid and burn‑wire actuation, and several rotational and linear assemblies. My focus was on resolving mechanical binding and tolerance issues: this involved transitioning from Delrin bushings to RC-fit linear ball bearings, redesigning friction interfaces using Delrin sleeves, and validating performance through CAD tolerance analysis and hands-on prototyping. The final system operated reliably through manual and sensor-assisted actuation, with significantly smoother motion and improved repeatability—positioned for full integration and further qualification testing.
My Role:
Systems Engineer
As lead of the damping subsystem for the Sierra Space debris-net launcher capstone, I managed the end-to-end development of multiple mechanical and sensor-driven assemblies, including linear and rotational mechanisms, burn-wire and solenoid actuators, and electronics integration. I focused on precision tolerance work by transitioning from Delrin bushings to RC-fit linear ball bearings, re-engineering friction interfaces with Delrin sleeves, and iterating designs using CAD, FEA concepts, and hands-on testing. The result is a fully assembled damping subsystem with smoother, more reliable operation that aligns with Sierra Space’s system performance goals and group design deck specifications.
My primary responsibilities centered on mechanical design, hardware integration, assembly, and feasibility testing within the damping subsystem. I designed and refined hatches, sliding forks, and track systems in SolidWorks, iterating part fits to account for thermal and travel tolerances. Recognizing binding issues in early builds, I replaced bushings with RC-fit linear ball bearings, optimizing bushing length and seat design. I also redefined friction surfaces by adding Delrin sleeves and adjusting preload, reducing drag and surface wear. Sensor integration involved both hall-effect magnetic sensors and reed-switch limit indicators, wired to board-level hardware testing and calibration. Throughout prototyping, I leveraged CAD analysis and FEA-like thinking to validate motion, torsional stiffness, and structural response, ultimately delivering a subsystem ready for testing within Sierra Space’s full launcher architecture.
My Components: Damping Subsystem
The damping subsystem assembly includes the Hatch Door Assembly, Linear Assembly, Rotating Assembly, Restraining Hook Assembly, and Burn Wire Assembly. The purpose of the damping subsystem is to dampen the rotation of the RSO around the tether axis (the major axis of the net launcher assembly). The Linear Assembly is designed to translate up and down, and it uses springs to increase or decrease the frictional force between itself and the Rotating Assembly through a frictional ring of HDPE plastic. The Rotating Assembly is able to rotate around and translate with the Linear Assembly. The Hatch Door Assembly rotates and translates with the Rotating Assembly, and it acts both as the lid of the net launcher assembly in its stored configuration and as a contact surface for the RSO to rest against and protect the vehicle during damping. Spring hinges are preloaded and act to force the doors open once an RSO has been identified for capture. Finally, the Restraining Hook Assembly is used to hold the assembly in place, therefore hindering any translational or rotational movement of the overall subassembly until the net launcher is in use, and the Burn Wire Assembly holds the Hatch Door Assembly shut in the stored configuration and allows them to open when desired.
Hatch Door Subassembly
The hatch door assembly serves two important purposes for the functionality of the net launcher design. Firstly, the bottom hatch door has a seal that is used to enclose the top of the net launcher from the surrounding environment and to act as a lid to keep the net inside the net retainer. Secondly, in the open configuration, the hatch doors act to increase the surface area in contact with the RSO when the RSO has been brought back to the net launcher and therefore as a protective barrier between the RSO and Sierra Space’s vehicle.
Linear Subassembly
The linear assembly is the sub-mechanism of the overall damping mechanism designed with only one degree of freedom: to translate in the direction of the net launcher boresight. This allows for the force of friction while damping the RSO’s rotation around the net launcher boresight to be modulated and controlled by the net launcher control system. The top plate is connected to guide rods traveling through Delrin bushings in our original design, and the bushings are press-fit into the bottom plate. This allows for translational motion of the top plate with respect to the bottom plate. The bushings have since been changed to flange-mounted linear ball bearings, which will be further explained below.
Design Iteration:
Original Design: The original design featured guide rods through manufactured Delrin bushings. Tolerances were based on binding analysis and consultation of Machinery’s Handbook.
Final Design: The final design featured off-the-shelf linear ball bearings with ground and polished steel guide rods traveling through them. Mounting and clearance holes were added to the static ring to accommodate this change.
Supporting Analysis: This change was the result of testing of the linear damping mechanism. Significant binding was occurring with the guide rods and bushings, and any load eccentricity resulted in immediate and not easily reversible binding. This issue was attributed to a lack of high positional tolerance from machining. The solution was to test linear ball bearings and offer clearance fits for the shafts of the linear ball bearings and for the flange mounting holes on the static ring. These clearances were RC clearances based on the Machinery’s Handbook.
Original Design: The original design featured 6061 Aluminum guide rods with an RC fit with the bushings as specified in the Machinery’s Handbook.
Final Design: The final design increased the length and material of these guide rods. The length was made longer so that the bottom of the rods do not rest inside the linear ball bearings in the linear damping assembly’s uncompressed state, and the material chosen was 6 mm diameter ground and polished stainless steel. A flat was added at the bottom for easier installation of the guide rods.
Supporting Analysis: Evaluation tools in the updated CAD model were used to find the minimum required length of the steel guide rods for use with the linear ball bearings. 6 mm ground and polished stainless steel was chosen for its diametrical tight tolerance to be used in conjunction with the 6mm inner diameter linear ball bearings.
Rotational Subassembly
The rotational assembly is designed to rotate around the linear damping assembly. During the second and final phase of the damping process, damping the RSO’s rotation around the axis of the net launcher boresight, the RSO will come into contact with the hatch doors (a subassembly of the rotational assembly as depicted below). At this point, the rotational assembly will match the rotation of the RSO and will rotate around the net launcher. It remains in contact with the linear assembly through the guide rods connecting the top and bottom plates and also bears against the frictional surface of the linear assembly. It’s through the interaction of the linear assembly with the rotational assembly that the only remaining axis of rotation of the RSO is dampened.
Design Iteration:
Original Design: The original design featured six 6061 Aluminum guide rods in rotational contact with the rings constituting the linear damping assembly.
Final Design: For the final design, the original 6061 Aluminum guide rods were turned down and Delrin sleeves were added to slide over them. Only three Delring sleeves and guide rod combinations were used as opposed to the original six.
Supporting Analysis: This design alteration was made as a result of testing the rotational damping assembly. The friction present in the system was too high due to tolerance stack-up and aluminum on aluminum grinding, and Delrin was chosen as the contact surface for the inner aluminum rings of the linear damping assembly and for rotating around the aluminum guide rod at its center. An RC fit was chosen for fitting the Delrin sleeves over the Aluminum guide rods, and the clearances were verified during manufacturing.
Burn Wire Subassembly
The Burn Wire Assembly holds the Hatch Door Assembly shut in the stored configuration and allows the hatch doors to open upon actuation by the control system. It utilizes a Nickel Chromium (Nichrome) wire which acts as a resistive heating element to burn through a nylon tiedown. Current is passed through the wire via actuation by the control system causing the nichrome to heat to temperatures exceeding 300 Celsius; the contact between the wire and the nylon tiedown causes the nylon to melt, releasing the spring actuated hatch doors.
Restraining Hook Subassembly
The Restraining Hook Assembly is used to hold the damping assembly in place, therefore hindering any translational or rotational movement until the net launcher is in use. It utilizes an electromagnetic solenoid to lock a spring-loaded hook in place. When the solenoid is activated, the spring rotates the hook backwards, releasing the damping assembly